Supply chain
Il concetto di Industria 4.0 promuove intensivamente l’integrazione di sistemi hardware e software, nonché di sistemi embedded, nelle supply chain, dalla materia prima al prodotto finito. L’obiettivo è quello di implementare un processo di trasformazione che porta i “vecchi” sistemi di produzione statici all’evoluzione in sistemi di produzione cyber-fisici che sfruttano soluzioni intelligenti.
Il percorso di “vertical integration” ha un enorme potenziale di ottimizzazione per la logistica e i sistemi di produzione. Se le procedure di produzione nel sistema ERP e nel controllo macchine degli stabilimenti sono tradizionalmente divise in aree spesso distribuite tra diversi sistemi IT, nell’industria che supporta i sistemi integrati i processi informatici e di comando vengono sincronizzati alle reti in modo da garantire accesso ai dati di produzione e logistici a tutti i reparti. L’effetto ottenibile è dunque quello di una “”horizontal integration” nell’intera struttura aziendale.

Approccio centrato sull’Industry 5.0
Le aziende che vogliono sviluppare i propri processi secondo i paradigmi dell’industria 5.0 devono focalizzare le proprie risorse sull’ integrazione, quindi devono integrare attività che hanno un’influenza reciproca sia tra di loro che con i soggetti che compongono la catena del valore.
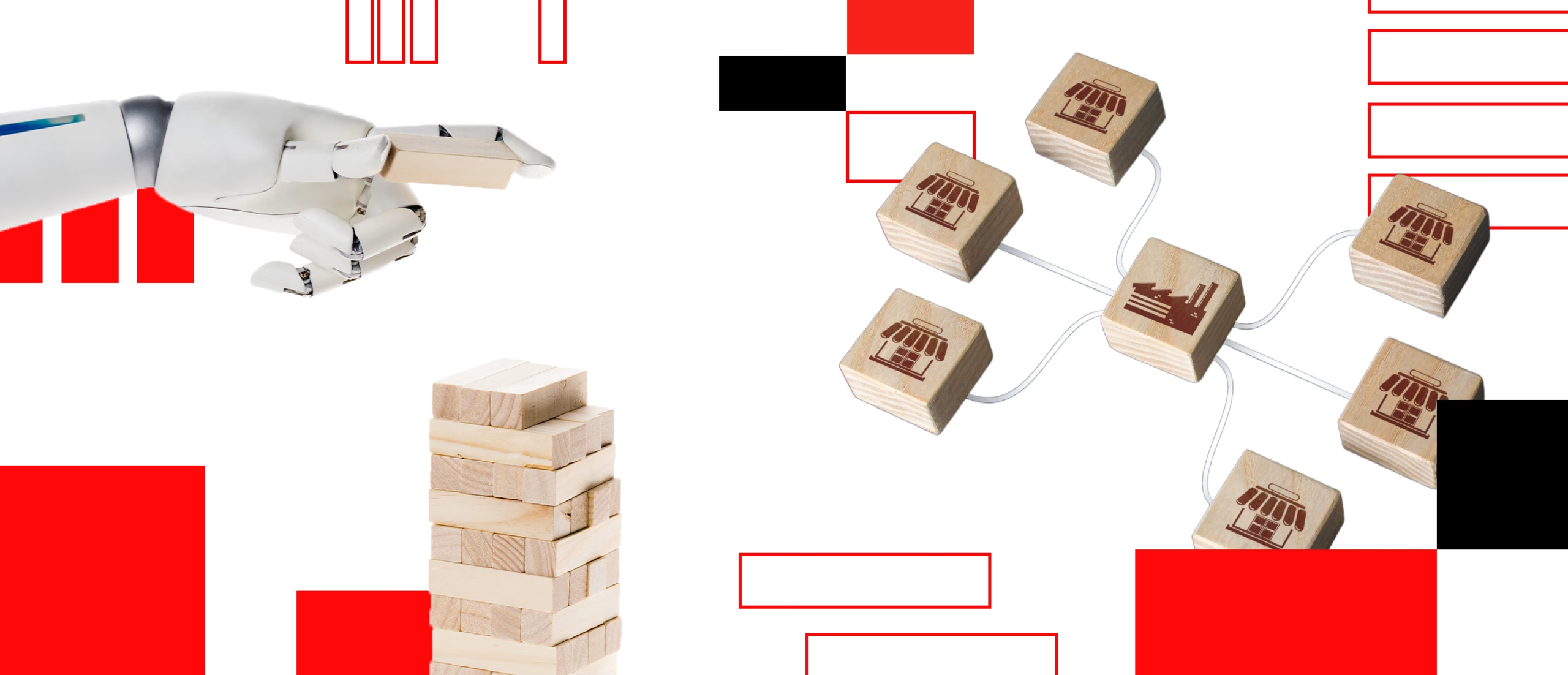
Interconnessione e integrazione di sistemi produttivi
Quando si parla di industria 4.0 ci si riferisce a un modello organizzativo volto alla produzione di beni e servizi attraverso una interconnessione e integrazione di impianti e macchine alle tecnologie digitali e alle persone.
La prima rivoluzione industriale è stata generata dall’adozione di macchine alimentate da fonti di energia inanimate come il vapore o i combustibili fossili, la seconda rivoluzione industriale dall’introduzione della produzione di massa, la terza rivoluzione industriale è quella veicolata dall’introduzione di impianti automatizzati basati sulle tecnologie elettroniche e informatiche, la quarta Rivoluzione industriale mira a integrare le tecnologie introdotte dalla precedente.
Tale obiettivo si può raggiungere grazie all’adozione di sensori installati sulle macchine e sugli impianti di produzione grazie ai quali siamo in grado di generare “trasparenza”, ovvero di rilevare parametri fisici e dimensionali di riferimento trasformati in dati in grado di essere elaborati e trasformati in programmi di pianificazione volti all’ottimizzazione dei processi, alla manutenzione predittiva, alla riduzione dei consumi energetici.
Il concetto di integrazione della parte “fisica” dell’azienda con i sistemi informativi usati si può applicare elaborando i dati disponibili trasformandoli in informazioni e dati interpretati, capaci di migliorare ad esempio la gestione dei magazzini, la produzione, le movimentazioni interne, ma anche gli acquisti a monte e le vendite a valle.
L’obiettivo principale è quello di creare sistemi produttivi, commerciali e logistici che siano in grado di gestire, interpretare e valorizzare la grande quantità di dati disponibili grazie all’utilizzo di tecnologie digitali.
I processi da attuare ed implementare per orientarsi al paradigma 4.0
Su base flessibile e rapida
La produzione deve essere organizzata in modo tale da garantire una personalizzazione di massa
(mass customization).
Su base a controllo totale
È fondamentale avere capacità di controllo sulle risorse al fine di evitare sprechi, massimizzare i profitti e operare considerando la loro razionalizzazione.
Su base in tempo reale
Le informazioni sui processi di produzione e sui prodotti devono essere completamente disponibili in real time.